Pilot Ladder Inspection Regime
Pilot ladders form part of a vessels SOLAS equipment, covered by the vessels Cargo Ship Safety Equipment Certificate and as such should be subject to regular recorded inspections as part of a vessels ‘Ship Management System’. Unfortunately the inspection regime of pilot ladders isn’t always as well guided and documented as it should be. Here we will consider exactly how, what and when pilot ladders should be inspected and why this is an essential part of pilot ladder safety.
From 10 July to 9 August 2023 the Paris Memorandum of Understanding (MoU) on Port State Control conducted a Focused Inspection Campaign (FIC) on Pilot Transfer Arrangements (PTAs).
One of their key findings was
Identification of ladders and record keeping of surveys and repairs were missing.
By having a documented, comprehensive and periodic inspection regime ships can guard against many of the deficiencies found by the Port State Control FIC.
Upon Delivery Of The Pilot Ladder
It may seem counterintuitive to be inspecting a brand new pilot ladder but this is one of the most important inspections a vessel will carry out on the pilot ladder. It can be tempting, for convenience sake to leave that brand new ladder wrapped up in plastic but apart for the need to inspect the ladder we need to remember the ladder is made of natural fibres and timber and as such is better stored where these components can ‘breathe’.
The reason we need to inspect a pilot ladder is two fold
- To reconcile the pilot ladder to the certificate to ensure the serial numbers, type and construction match
- To inspect the quality of the pilot ladder and ensure you got what you paid for. As we have mentioned before the market is currently flooded with counterfeit ladders so it’s better to spot this sooner rather than later.

When inspecting the pilot ladder it should be rolled out on deck so that it can be inspected throughout it’s length from thimble end to seizing end. The first thing to do is to reconcile the ladder with the certificate. We need to check both the upper (an if fitted lower) ID plates. These are usually found on the bottom of the uppermost step and bottom of the lowermost spreader (if fitted). We need to check
- The serial numbers all match up
- The length of the ladder corresponds with the certificate
- The construction matches the certificate
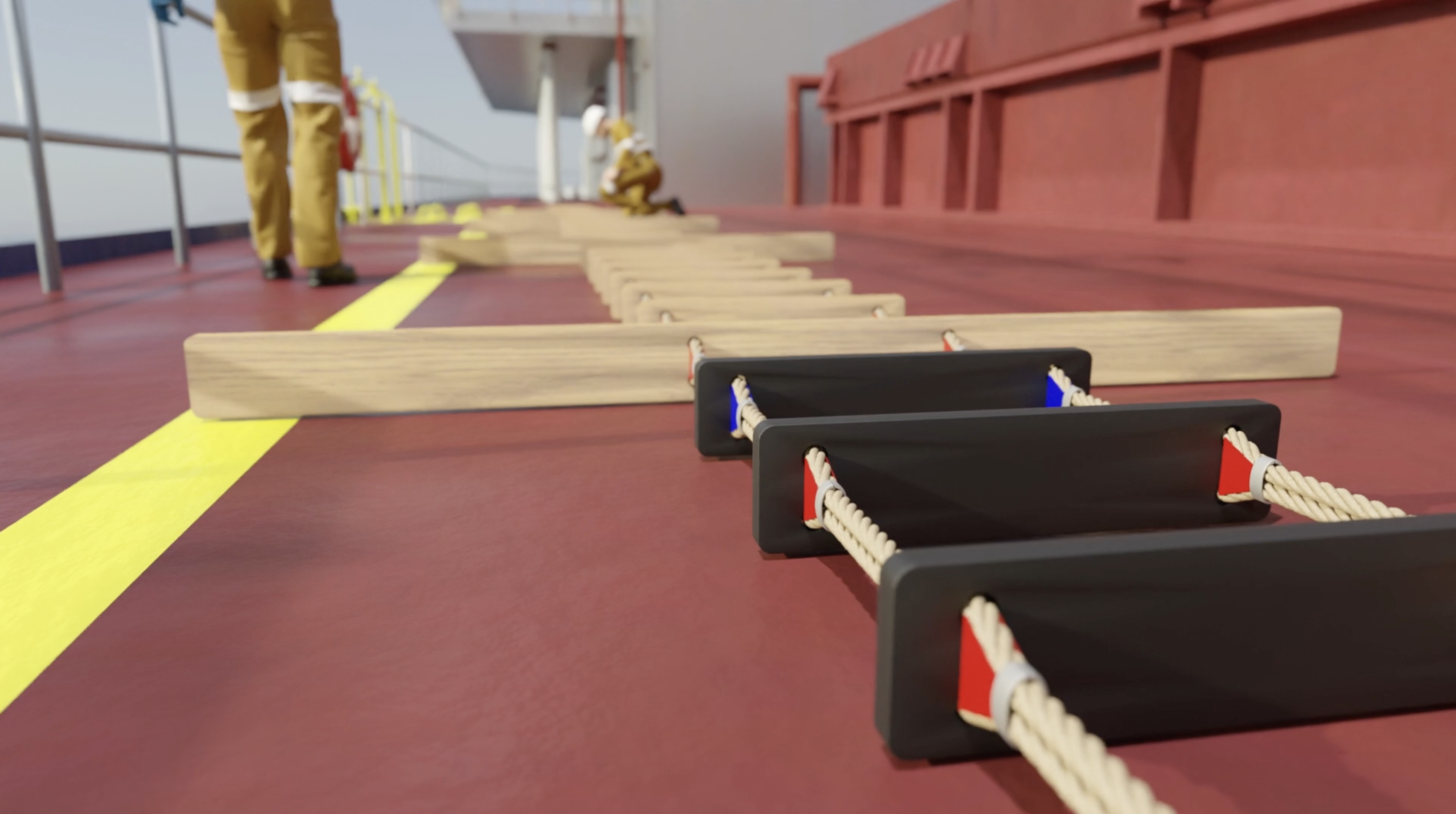
We recommend that the location of the ladder be reconciled with the certificate. Rather than writing on the certificate we recommend storing the document in a plastic wallet with the location of the ladder indicated on the plastic wallet (for example Port Winch, Starboard Winch, Spare – Bosuns Store FWD) this means if you are ever asked to produce a certificate for a particular ladder this can be done without confusion or delay.
Certificates should be stored in the vessels certificate file and be available for inspection by pilots, surveyors and Port State Control inspectors upon request.
After reconciling the certificate it’s important to check the pilot ladder is of good quality as this will indicate it’s authenticity. Are the materials used of a high quality, are ferules or hand seizings made up in a secure manner such that the wedges cannot be pulled out of the steps. Are the ropes of good quality, are the steps made from knot free hardwood and free from any varnish or paint (counterfeits are often dyed a darker colour to give the impression of heat treatment).
Once you are happy you have been supplied with a quality pilot ladder it should be rolled back up, secured in a seamanlike fashion and stored appropriately. This should be in a well ventilated storage locker, clear of the deck (sitting on a pallet is fine) and NEVER in the same area as chemicals, paints or cargo handling equipment. Contamination is the greatest danger to the integrity of your ladder due to the natural nature of the components. The ladder should be out of the way so that it isn’t being knocked or constantly moved around whilst in storage as it may well spend some considerable time in storage.
If you are receiving a PTR Holland ladder it is important the instructions are followed to register the ladder against the vessel on their database. Not only does this make it simple for pilots and authorities to check the vessels ladders it also entitles the ladder to a FREE 30 month load test.
Prior To Use Pilot Ladder Check
Prior to use a responsible officer needs to inspect the pilot ladder to ensure it is fit for use with a Pilot Ladder Pre-Use Inspection. For winch stowed ladders this can be done as the ladder is slowly deployed and for non-winch pilot ladders the ladder should be laid out on deck.
The key aspects we need to consider are
- Is the pilot ladder older than 30 months (the date of manufacture is on the ID plates)? If so has there been a pilot ladder load test and certificate issued?
- Does the ladder have any damage. We are looking for deformation of the rubber steps, splits, cracks or damage to the rungs and spreaders.
- Is there any damage to the ferules, wedges and seizings giving rise to loose steps and spreaders.
- Do the steps and spreader lie horizontally when the ladder is deployed.
- Do the side ropes show indications of damage or rot. This is especially important where the ladder meets the deck edge (where a rounded skid plate should be fitted).
- Has the pilot ladder been repaired how many replacement steps are in use (maximum is 2)
- Ancillary equipment including securing ropes, manropes, lifebuoy with self illuminating light, handhold stanchions and any bulwark ladders should also be given a thorough check.
Post Use Pilot Ladder Check
Upon completion of pilot transfer it is essential that the pilot ladder is again checked for damage with a Pilot Ladder Post Use Inspection. Spotting the issue now means it can be rectified before the next time the ladder is required when it may be too late to correct.
Again we are looking at
- Steps, spreaders and in particular the bottom 4 rubber steps show no indication of damage.
- The steps and spreaders are still sitting horizontally
- The step fixtures are still in good condition and holding the pilot ladder steps firmly in place
- The clamps or seizings are still in good condition
- If any step has received damage and requires replacement this should be done in accordance with the manufacturers instructions and a record of this replacement and when it was carried out needs to be stored WITH the certificate.
- If the pilot ladder has become contaminated it should have a fresh water wash down
- Ensuring the pilot ladder is allowed to air dry prior to storing and/or covering to prevent mildew or rot forming.
By having a documented, comprehensive pilot ladder pre and post use inspection regime, pilot ladders should have a long and most importantly safe lifespan.
Periodic Onboard Pilot Ladder Inspection
Every 3 months the vessels pilot ladders should be inspected by a ‘Senior Officer’ (Chief Officer or Master) and these inspections documented for EACH pilot ladder held onboard, including spare ladders.
Prior to conducting the Pilot Ladder 3 Month inspection the manufacturers pilot ladder documentation should be consulted for any recommended inspection checks.
In order to carry out these inspections, winch deployed ladders must be removed from the winch and laid out on deck.
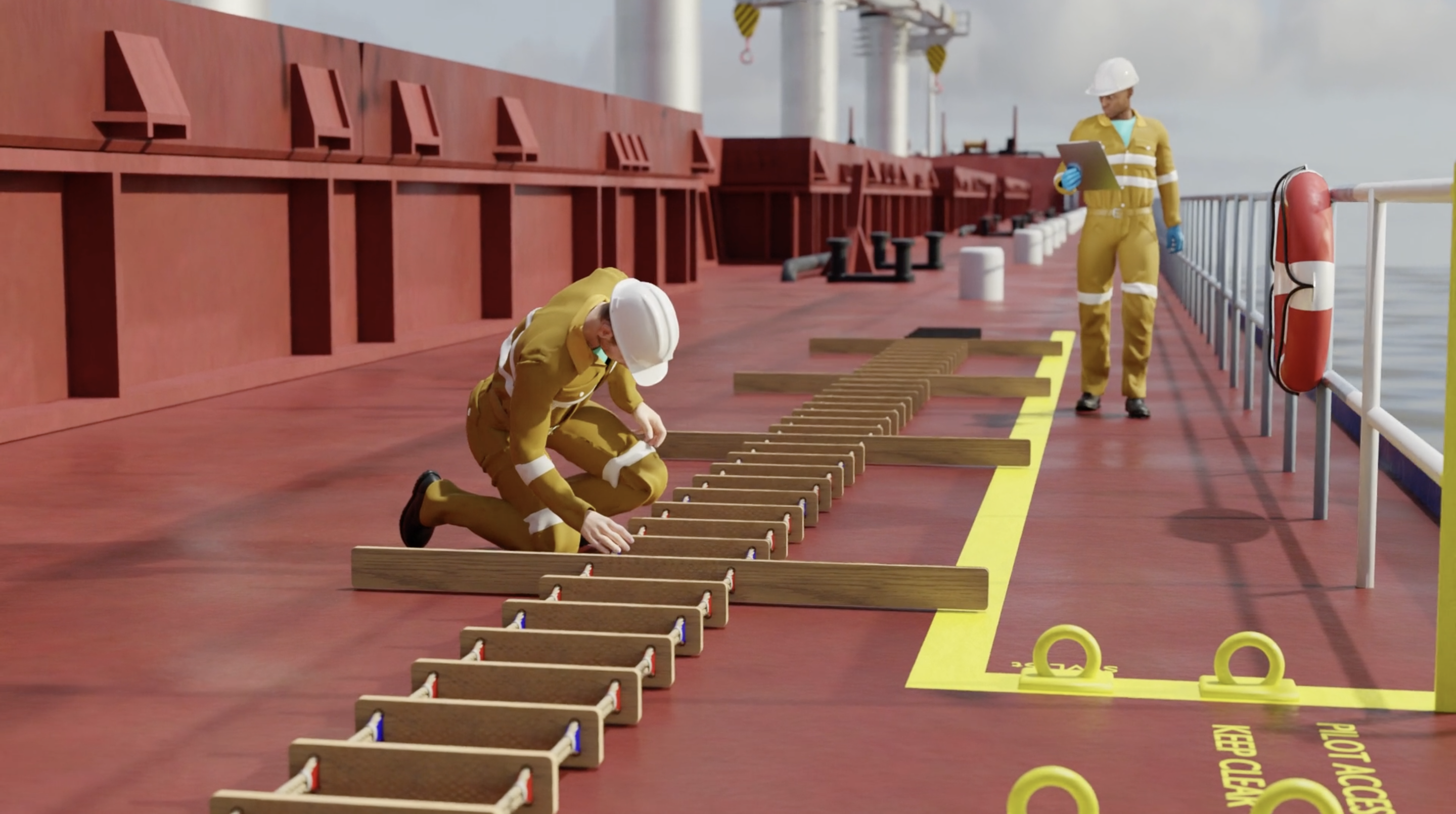
The 3 monthly inspection should be a much more thorough inspection of each and every component making up the pilot ladder. The lay of the ropes should be untwisted in a number of areas to check for the presence of rot or mildew and the clamps, seizinings and wedges should each be inspected in detail for damage. In this inspection the items we look to cover are
- The ladder should be reconciled against the certificate and the serial numbers should match with certificate and top and bottom ID tags (where fitted). The ladder should be under 30 months old, or if over 30 months old shall have a retest certificate issued by the manufacturer or approved testing station.
- Steps should be horizontal and equally spaced
- Side ropes are clean and in serviceable condition. No knots splices or joints (except above the top step if manufactured in that manner.)
- Steps are not cracked/broken or warped or worn. Steps are clean and free of paint, pro¬tective coatings or dirt that will inhibit the non-slip capability of the steps
- Number of replacement steps (maximum of 2):
- Step fixtures are secure and tight.
- Clamps or seizings securings are in good condition
- Is the pilot ladder stored in accordance with the manufacturer’s instructions?
- Are the manropes, securing ropes and anciliary embarkation equipment in good order
- Are the certified deck strong points in good condition and appropriately marked with their Safe Working Loads
- Are any handhold stanchions in good condition and capable of being fixed to the deck and at a higher point so that they are FIRMLY held in place.
- Is the pilot transfer area marked on deck with appropriate text to indicate the area should be free from obstructions.
- If used is the ships accommodation ladder in good order, are the falls in good condition and in certification. Is the bottom platform capable of being firmly secured at a range of angles.
Upon completing the inspection the senior officer should certify the pilot ladder as being fit for ongoing use and the record of this inspection and declaration of conformity be documented as per the vessels SMS.
Annual Flag State Inspection Pilot Ladder Inspection
There shall be an annual inspection by the flag State or Classification Society surveyor. The flag State or Classification Society will usually use its own checklist but such an inspection should include.
- Does the certificate correspond to the pilot ladders ID plate(s)?
- Are the manufacturers maintenance instructions available onboard the vessel?
- Is the ladder stored in a seamanlike manner in accordance with the manufacturers instructions?
- Are steps horizontal and evenly spaced (330 mm +/- 20 mm between steps)?
- Steps are not cracked, broken, warped or worn. The steps are clean and free of paint, varnish, protective coatings or dirt that will inhibit the non-slip capability of the steps. Timber steps are free of knots.
- Number of replacement steps (maximum of 2)
- Have the replacement steps been fitted as per manufacturer’s instructions and has this been properly documented?
- Step fixtures are secure and tight.
- Side ropes are in good condition and show no signs of wear, damage, rot or mildew.
- Seizings/step securing are in good condition, paying particular attention to the termination below the bottom step. Is the side rope tightly wound around a step fixture or fitted with a double seizing and suitably whipped to prevent fraying?
- The ladder is fitted with a legible identification plate beneath the top step and lowermost spreader.
- Are the manropes, securing ropes and ancillary pilot transfer equipment in good order
- Are the certified deck strong points in good condition and appropriately marked with their Safe Working Loads
- Are any handhold stanchions in good condition and capable of being fixed to the deck and at a higher point so that they are FIRMLY held in place.
- Is the pilot transfer area marked on deck with appropriate text to indicate the area should be free from obstructions.
- If used is the ships accommodation ladder in good order, are the falls in good condition and in certification. Is the bottom platform capable of being firmly secured at a range of angles.
Again this inspection must be documented and a copy stored onboard for inspection by a relevant party.
By carrying out a frequent, structured and well documented pilot ladder inspection regime a vessels pilot ladders will be capable of providing a safe means of access to and from the vessel. Additionally this documentation is vital should a vessel ever experience an issue with her pilot transfer arrangements to demonstrate every effort was being taken to provide safe and compliant pilot ladder access arrangements.
Ladder inspections should be treated as importantly as all LSE inspections. Pilot ladder incidents resulted in 7 fatalities in 2023 and multiple injuries. Whilst pilot ladder transfers are in the main a safe and efficient method to embark or disembark a pilot the potential for serious injury or fatality when things go wrong should always be in the forefront of seafarers minds.
Fathom Safety can help in ensuring pilot ladder safety by providing comprehensive pilot ladder training and our pilot ladder management service can ensure your fleet always has premium quality, in date and properly inspected ladders. Our end to end pilot ladder management service is saving our client thousands of dollars in pilot ladder procurement and prevented delays, fines and inspections. Let us take the stress out of pilot ladder transfer with our superb white glove pilot ladder service.
This article should be used as a guide and used in conjuction with the relevent SOLAS, ISM and ISO regulations and standards.